Little's Law
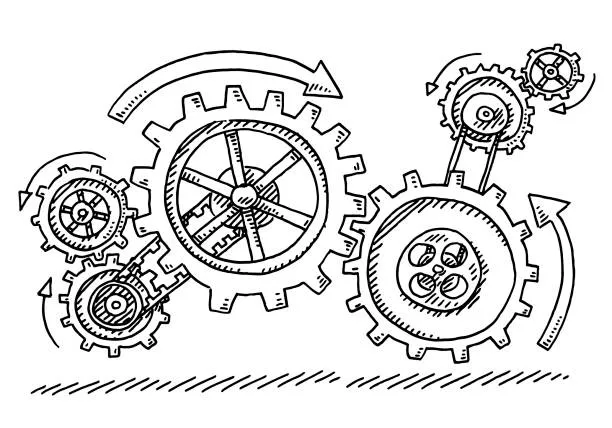
Delving into the intricacies of complex systems often reveals foundational principles that capture their core essence. Littleās Law, stemming from a branch of operations research called Queueing Theory, serves as a prime example. This principle, named after MITās Professor John Little, intricately connects processes, workloads, and outcomes, highlighting the crucial balance underpinning efficient operations.
I wrote a post on this topicāon its application to the Scalability and Fault Tolerance of modern web applications. In this piece, I provide a more accessible introduction, detailing its relevance to everyday life and management practices.
Littleās Law Simplified
In its most basic form, the law can be represented as:
- Lead Time: The duration required for an item to traverse and be completed within a process.
- Work In Progress (WIP): Imagine looking into a process pipeline, much like peering into a transparent tube. If you spot, say, 10 ongoing tasksābe it applications, requests, or products being craftedāit signifies that there are 10 units currently being processed. This count of active tasks is the Work in Progress.
- Throughput Rate: This denotes the average number of items that accomplish their goal within a set time frame, perhaps an hour or a day.
Letās explore a few practical examples where the concept of lead time sheds light on Littleās Law and its implications.
Process Pipeline
Suppose thereās a factory assembly line (our process pipeline). If 25 widgets are in different stages of assembly and 5 get completed every hour, the lead time can be calculated as:
If we suddenly introduce 25 more widgets to this line without any change to the process or throughput rate, our lead time grows:
This shows that simply increasing the workload without enhancing the process can lead to inefficiencies, longer wait times, and potential bottlenecks.
Traffic Congestion
Think of a highway during rush hour. Each car represents a unit of work, and the highwayās capacity is like the throughput rate. If the highway can handle 1,000 cars moving smoothly per hour, and suddenly 2,000 cars are on the road, the travel time (lead time) for each car doubles. Just as adding lanes or implementing carpool policies can improve the flow, in a process pipeline, one must improve the throughput rate or limit the WIP to manage the lead time.
***
Managerial Insights
The implications for management are significant. If minimizing lead time is crucial for us and our clients, we must either:
- Boost the throughput rate of the process. This might involve streamlining operations, investing in faster machinery, or training staff.
- Limit the WIP. This could be achieved through strategic decisions like scheduling breaks in production or, in the case of our highway analogy, introducing tolls or carpool lanes to manage flow. In extreme cases, it could also mean declining new business if capacity is reached.
One thing to note is that the application of Littleās Law requires a stable system. Itās less pertinent in chaotic or start-up environments. Moreover, the law assumes a non-preemptive process, meaning every task in the queue gets equal treatment and no task can skip ahead.
In conclusion, Littleās Law offers profound insights, and its understanding can be a game-changer in various fields, especially in management. It emphasizes the interconnectedness of processes, workloads, and results, reminding us of the importance of balance and efficiency.